Safety is our First Priority
.png)
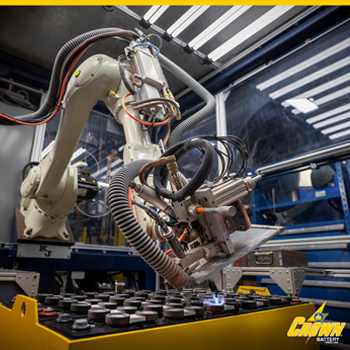
.png)
HERE ARE 9 WAYS WE PROTECT OUR EMPLOYEES AND OUR COMMUNITY:
Rule #1: Create good, safe jobs — and automate manufacturing stages to reduce risk
Many suppliers outsource production to the lowest bidders with lax laws, substandard safety equipment, or unregulated labor conditions.
By contrast, Crown Battery provides good pay, benefits, and a safe work environment to our employees.
We’ve been making batteries in the USA since 1926… and we’ve stayed in the USA because regulation drives some of the world’s highest standards for worker safety, environmental protection, and quality.
Today, we continue to automate manufacturing stages to increase safety. (Keep reading to see how.)
Rule #2: Invest heavily in comprehensive, state-of-the-art engineering controls and other safety equipment
Engineering controls are typically systems whose main job is protecting workers.
Crown’s multimillion-dollar safety systems include engineering controls such as dust collection systems with advanced HEPA finish filtration that’s 99.97% efficient at removing airborne particles 0.3 microns or smaller.
In addition, wastewater undergoes a 19-step filtration process that includes precipitation and reverse osmosis to capture contaminants and recycle water.
Rule #3: Stringent safety training is continuous
Crown Battery’s programs are mandatory and include:
- Company-wide Safety Training Day covering vital safety topics
- Ongoing educational programs and hands-on training
- New-hire safety orientation covers topics such as personal protective equipment (PPE) and other safety policies, along with classroom, hands-on, and follow-up training
Rule #4: Share safety feedback and criticism openly – and anonymously
Any employee can write directly to Crown Battery’s President/CEO, Hal Hawk – simply by dropping a letter in our “Letters to Hal” box.
Employees can decide whether to include their name or remain completely anonymous.
Hal personally reads each suggestion and helps ensure they’re part of constant improvement plans, including safety program updates and equipment upgrades.
Rule #5: Give people the best safety equipment possible
We’ve spent millions of dollars meeting and exceeding best practices for safety equipment, such as:
- Issuing all plant employees a half-mask or full-face respirator with P-100 cartridges that guard against exposure to potential hazards – and requiring their wear as needed
- Supplying and requiring PPE like hard hats; eye, face, and hearing protection; and gloves and footwear that meet or exceed job requirements
- Providing and laundering company uniforms for all manufacturing jobs
In addition, employees are required to wash their hands before starting their shift, before and after breaks, and before leaving the plant. And certain positions require showering after shifts.
At our headquarters / manufacturing plant, a full-time, onsite, registered nurse (RN) monitors employees’ health. And Fremont Promedica 360 provides supplemental, onsite nursing support every month.
Rule #6: Audit for safety and compliance – and collaborate with regulators
Trained employees double-check hundreds of items, from critical safety equipment to training certifications and signage, hand guards, fall restraints, storage and security systems, and more.
In addition, volunteers on all three shifts have been certified in First Aid, AED use, CPR, and spill cleanup – and these items are routinely inspected and maintained.
We also work closely with regulatory agencies and third-party safety and environmental experts – to protect employees and help meet or exceed all federal, state, county, local, and industry best practices for safety equipment, environmental protection, engineering controls, training, and more.
Rule #7: Ethically source raw materials
We ethically source raw materials -- primarily from domestic suppliers – and ensure our domestic batteries are responsibly recycled. This helps protect workers and our environment across the supply chain.
In addition, we minimize mining for raw materials by sourcing ~80% previously recycled materials for our batteries.
Rule #8: Give every plant employee stop-work authority
It’s simple: Anyone working at our plant has the authority to stop their assembly line, production stage, or the entire plant – to prevent unsafe working conditions.
We encourage and reward this. Because after all, nobody knows their job better than the people doing it.
Rule #9: Keep improving constantly
Throughout our company, we regularly review, refine, and improve our best practices, safety protocols, training programs, safety tools, and engineering controls.
And we continue to make multimillion-dollar investments in plant and equipment, such as a brand-new robotic cell assembly production line.
Over the past two years, we have developed plans to further reduce risk, including adding automation to all four Pasting lines and enhancing indoor air quality.
These capital improvement projects help us minimize our environmental impact…
… increase product quality and lifespan…
… and most importantly, continue to enhance our employees’ safety.
Because “Safety First” isn’t a destination or a marketing slogan – it’s thousands of steps and projects, big and small, to keep getting better… and protect our employees, our community, and our environment.
Learn more about Crown’s recent safety programs here: Crown Battery Creatively Engages Employees in Safe + Sound Week 2022 Events
.png)
.png)
.png)